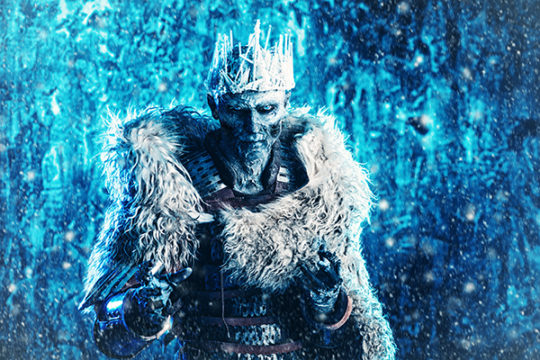
We all know Game of Thrones, the hit series currently in its final season on HBO, is really about hazmat transport. Fittingly, Sunday night’s episode 3 supplied a metaphor that every supply chain organization should take to heart.
Spoiler alert: If you aren’t current on Game of Thrones, skip the next two paragraphs!
The episode was one long battle between the undead forces of the Night King and the human race, making its last stand at Winterfell. With his ability to raise fallen humans and command them to fight on his side, the Night King was on the verge of final victory.
Then, a single oversight in his personal defenses left a gap, which a human exploited. In one stroke, it was all over. The Night King and his army were obliterated.
Imagine your operation is the Night King’s army
Your team members probably look like White Walkers before they’ve had their first cup of coffee, right?
Anyway … imagine your operation is enjoying success and things are generally going your way. You do your best to make sure you ship Dangerous Goods compliantly, not just because it’s the law but because you know it makes the supply chain safer for everyone. To get back to the analogy, you’re the Night King, and compliance is the defense that keeps you safe from humans.
Can a single compliance gap destroy everything?
Barring an unprecedented disaster, the answer is no. No single mistake will end your operation. However, compliance gaps can hurt your operation more than you might think—and most operations don’t even account for the multiple costs of even relatively minor compliance errors.
One compliance gap; five “dominoes” of potential costs
Some of the costs of non-compliance—fines and civil penalties—are obvious. In fact, some shippers (and we hope you’re not one of them) just consider these a cost of doing business.
But compliance errors and gaps can trigger a domino effect beyond the obvious costs. These fall into five categories:
Domino #1—Penalties and fines: Of course you know the U.S. DOT (or other governing bodies) can assess civil penalties if a shipment is found to be non-compliant—and they can be significant. But carriers such as FedEx and UPS also assess fines, and some supply chain partners also have penalties built into their contracts.
Domino #2—Supply chain disruption: Non-compliant shipments get stopped and delayed. You might have to cover return shipping costs and/or the costs of replenishing the supply chain for seized or damaged items. Plus, you have to devote extra time and manpower to getting the shipment right and making your customer happy.
Domino #3—Strained relationships: Mistakes happen, but a compliance gap in your operation can lead to multiple mistakes, and that can damage your reputation. The difference between 99.9% on time and 99% on time can be one fewer customer.
Domino #4—Making it right: If there’s an actual incident, you might have to cover damage or contamination of trailers, tankers, containers or vehicles, plus disposal costs, incident reporting and cleanup costs—not to mention potential liability for damages or injuries.
Domino #5—Long-term hangovers: One incident can generate bad publicity and trigger higher insurance premiums. You might also need to pay for added training, documentation and processes to address the compliance gap that led to the incident.
Will one mistake set all these dominoes in motion? Probably not. Should you do everything you can to minimize the risk of mistakes happening? Ask the Night King.
How to protect your bottom line from compliance errors
You can never eliminate every potential hazmat compliance error, but Labelmaster offers several ways you can reduce their potential to hurt your bottom line:
- DGIS—the industry’s most robust, flexible, advanced hazmat shipping software—validates shipment data instantly against an internal rules engine updated whenever a significant regulation changes.
- Labelmaster online training courses don’t just “check the box” for required training but give your teams the knowledge they need to ship hazmat compliantly.
- Labelmaster Services experts work like an extension of your team to make your operation more efficient, more compliant and more profitable.
- A Total Value of Compliance Assessment helps you determine the complete costs of non-compliance across your operation so you can persuade your management that improved compliance is worth pursuing.
Don’t take compliance for granted. The better prepared your operation, the less likely a single compliance gap will leave you on the wrong end of a dragonglass dagger.
Labelmaster is a full-service provider of goods and services for hazardous materials and Dangerous Goods professionals, shippers, transport operators and EH&S providers. See our full line of solutions at labelmaster.com.