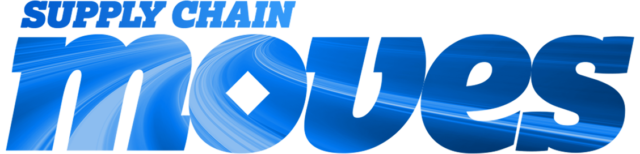

Week of August 3rd, 2020
Linking technology news with Dangerous Goods compliance
The COVID-19 pandemic has emphasized the critical role technology plays within the supply chain. And for some, it has placed a spotlight on the need for greater investment in technology moving forward.
To help companies keep a pulse on technology trends impacting business and the movement of dangerous goods throughout the supply chain, Labelmaster has launched “Supply Chain Moves,” a bi-weekly report linking the latest technology news to dangerous goods compliance.
Let’s examine the recent supply chain technology and industry news.
TECHNOLOGY
- Labelmaster Survey Examines Impact of COVID-19 on Hazmat Supply Chain: Global survey of dangerous goods professionals identifies the need for remote training, upgraded technology and more effective communication of data.
- Supply Chain Resiliency Begins in the Cloud: As our lives and work continue to adjust, it’s important to retain the many lessons the pandemic has taught us and think about how we can build more resilient supply chains.
- Why Supply Chain Visibility is Key to APAC Retailers: Having complete visibility over the supply chain will enable retailers to tide over the Covid-19 pandemic and transform their businesses.
- Omnichannel Technology – A Holistic Approach to Retail?: Imagine a fully integrated experience in which the customer journey is seamless and pleasurable. There are already a number of futuristic technologies that can make this a reality.
- The Pandemic has Complicated the WMS Procurement Process: Vendors and warehouse managers typically use multi-day conferences and whiteboarding to buy and implement warehouse management software. The pandemic has turned that process upside down.
3PL TECH
- The TMS Outlook: 2020 Update: ARC Advisory Group examines the latest Transportation Management Systems trends and that the impact COVID-19 has had on the market.
- GlobalTranz Launches Final Mile Offering: Provides shippers with an intuitive, technology-enabled final mile solution that creates efficiencies, reduces accessorial charges, and delivers a superior customer experience.
- 3PL vs. 4PL vs. 5PL – Here’s the Difference: Food Logistics breaks down the difference between 3PLs, 4PLs and 5PLs and why these partnerships matter, especially in a time of crisis.
Technology & Dangerous Goods Compliance
The COVID-19 pandemic has greatly impacted the global dangerous goods supply chain. Yet even as the industry has shown tremendous resilience, this crisis has shed light on weaknesses related to DG organizations’ ability to keep shipments safe and compliant, and the need for further investment in DG training, technology and infrastructure.
This was evident in the 2020 Global Dangerous Goods Confidence Outlook, which surveyed 258 DG pros from around the world about the impact of the COVID-19 pandemic on their organizations and the changes needed to their DG management operations moving forward. According to the survey:
- The top supply chain management challenges were receiving goods on time (82%), receiving complete and timely information from partners (75%) and lack of carrier availability (73%)
- The top challenges directly related to DG management were re-certification of employees (69%), training employees on regulations (68%) and changes in rules related to the pandemic (57%)
As organizations work towards a state of normalcy within their operations, it will still likely be a “new normal.” Given the supply chain challenges spotlighted during the pandemic, it’s clear to DG pros that their organizations must address gaps—specifically those related to data accuracy and completeness, as well as more effective tools for training team members remotely.
- 88% of respondents said “accurate and complete DG shipment data” is important to the future of their organization, while 74% said that about “more effective remote DG Training.
- But getting the resources they need may be a challenge. While a quarter of respondents believe that their companies are likely to spend more on DG management as a result of the pandemic, 59% said the investment will stay the same, and 7% expect it to decrease.
The COVID-19 pandemic has shone a spotlight on areas of DG management that must be addressed within many organizations. As they look to move forward in the ‘new normal,’ it is important for senior leadership to recognize the critical role that DG management plays in maintaining a smooth, resilient and compliant supply chain, and that it can actually be a competitive advantage that drives revenue, reduces risk and enables better customer service. Then they must invest in the technology, training and infrastructure that DG pros need to manage DG effectively and efficiently.
Learn more about how COVID-19 has impacted the DG supply chain, and the changes DG pros feel are needed within their organizations, by downloading the 2020 Global Dangerous Goods Confidence Outlook: https://www.labelmaster.com/dg-confidence-outlook.
To learn more about dangerous goods software or how to establish a safer, more compliant supply chain, visit https://www.labelmaster.com.
Have questions about dangerous goods transport? Call the Labelmaster Regulatory Hotline at 1.800.621.5808.
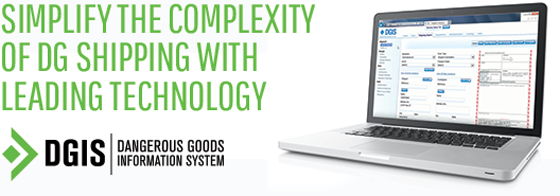
Labelmaster’s Dangerous Goods Information System (DGIS) is the leading SaaS solution to help companies more efficiently and accurately manage their Dangerous Goods shipments. DGIS validates your Dangerous Goods shipment data against the latest regulations, ensuring a more efficient supply chain and reducing friction found in Dangerous Goods shipments. DGIS is a certified partner/validation solution with ERP, transportation and warehouse management systems.
