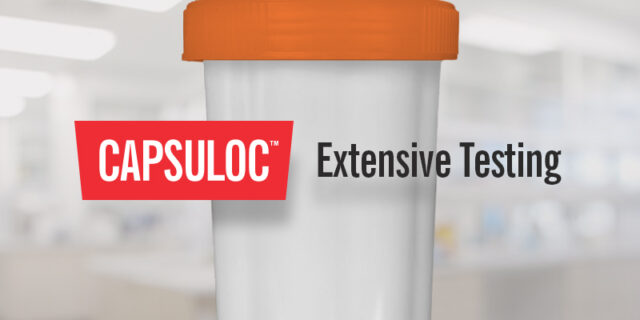
New ideas in Dangerous Goods packaging don’t come along very often. And when they do, they get a lot of extra regulatory scrutiny.
Take secondary hazmat packaging kits. For decades, the only option available was the metal can, and all the packaging regulations providing exceptions were written with metal cans in mind. So, when we introduced Capsuloc™—an innovative new secondary hazmat container, constructed from plastic—we knew PHMSA was going to look at it very, very closely.
In May 2023, PHMSA issued Special Permit DOT-SP 21488, which gives Capsuloc relief from regulatory burdens similar to the relief other exemption packagings with metal can containers receive. Here’s a look at the extensive testing that was required to earn this Special Permit. Capsuloc is also accepted as exemption by UPS and FedEx.
What makes Capsuloc a different—and better—secondary hazmat container?
Labelmaster Sr. Packaging Product Manager Bill Barger envisioned a metal can alternative years ago. “Customers would say how dissatisfied they were with the effort that it takes to put ring locks on metal can containers, and they’d complain about trouble taking the rings off,” he says. “I just thought to myself there has to be a better way.”
Barger’s idea became Capsuloc. Here are a few ways it’s superior to metal can-style secondary containers:
- Its screw-tight lid is easier and more secure than metal can lids, which need to be pried open and pounded closed.
- It requires no ring locks.
- It’s more durable and more re-usable than metal cans.
- Its kits are 32% lighter than metal can kits.
Until now, however, many metal can exemption kits had a small advantage—special permits that removed some regulatory hurdles. But Special Permit DOT-SP 21488 gives Capsuloc that same advantage. You can now use Capsuloc in most of the same Dangerous Goods transport workflows as metal can exemption shippers—with advantages metal cans can’t match.
Skeptical? Check out these test results that convinced PHMSA.
The vibration test: Capsuloc won’t back off
The first test was a vibration test, where Capsuloc containers (packed, as they would be in transit, with absorbent and a glass bottle filled with liquid) must withstand vibrations designed to simulate conditions of travelling one hour by truck and two hours by air.
Barger explains, “What we’re trying to do here is eliminate the need for a customer to put a piece of tape on the lid to keep it from backing off,” or becoming less tight. “We were trying to prove that the container doesn’t back off with the quad ring that we use. The testing lab calls it the ‘O-ring on steroids.’”
Capsuloc containers were subjected to three, 3-hour tests—nine hours of vibrations. And all three screw-top lids remained exactly where they started. “Usually when you put a closure on a container, it’ll back off by a certain percentage without any vibration just by sitting there overnight,” says Barger. “But there wasn’t any movement of the closure after nine hours of vibration testing.”
As a result, Special Permit DOT-SP 21488 permits use of Capsuloc without applying tape to the container lid.
The pressure differential test: Capsuloc refuses to fail
We designed Capsuloc containers to perform better than metal can alternatives, but that performance had to be proven through lab testing. Hence, the pressure tests.
Barger explains, “What they do is they fill the container with water and pressurize it through a hole in the bottom. They start at 100 Kilopascals (kPa) and then every five minutes they raise it by 10 KPA until it fails.”
Metal can containers tested at the same time began to leak through their ring locks at pressure as low as 110 kPA, with the best lasting until 130 kPa. But “the Capsuloc container got up to 250 kPA before they turned the machine off,” says Barger. “It didn’t even fail. It didn’t leak, didn’t do anything.”
As a result, Special Permit DOT-SP 21488 permits use of Capsuloc for the transport of toxic inhalation hazard and pyrophoric materials. Also, passing these tests allows shippers to use any inner bottle up to 1 liter by air—even if their bottle isn’t capable, or hasn’t been proven to pass the pressure test itself—as long as it’s compliantly packaged in a Capsuloc kit.
The penetration test: Capsuloc crushes the metal can
The penetration test drops a 15 kg steel dart onto the container from heights starting at 40 inches. The test is done on the lid of an upright container and also on the side of the container. During Capsuloc testing, the dart penetrated both the pint can lid and the Capsuloc lid from 40 inches.
The side penetration test was another story. The dart crushed the metal can from 40 inches, but the Capsuloc container survived drops from as high as 70 inches with denting but no penetration.
“So, from a side impact—which is your most common incident by a forklift in a warehouse—a metal can will not hold up,” says Barger. “Capsuloc is going to give your shipment a better chance of surviving a side impact.”
As a result, Special Permit DOT-SP 21488 permits use of Capsuloc kits (when properly assembled and closed in its UN-specification packaging) for many hazard class 3, 4, 5, 6, 8 and 9 shipments without hazard labels or placards.
Ready to try Capsuloc?
Is Capsuloc a fit for your operation? Call the experts at Labelmaster to discuss your materials, your workflows and all the details that go into making the best packaging decisions.
Now that it’s been passed these extensive tests to secure Special Permit DOT-SP 21488, Capsuloc is the most efficient, most versatile secondary containment system available.
Make sure your shipments are safe and in complete compliance with a full line of solutions from Labelmaster—a full-service provider of goods and services for hazardous materials and Dangerous Goods professionals, shippers, transport operators and EH&S providers.