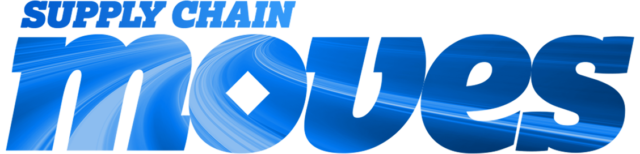

Week of February 1st, 2021
Linking technology news with Dangerous Goods compliance
As companies continue to adapt to the changing supply chain landscape, many are turning to innovative technologies, new processes and other value-added services to help keep pace.
To help companies keep a pulse on technology trends impacting business and the movement of dangerous goods throughout the supply chain, Labelmaster has launched “Supply Chain Moves,” a bi-weekly report linking the latest technology news to dangerous goods compliance.
Let’s examine the recent supply chain technology and industry news.
TECHNOLOGY
- How New Tech is Transforming the Retail Supply Chain: While e-commerce sales surged, a significant amount of money was wasted due to inefficient processes, damaged items, returns and more. However, the right technology can help your business navigate these challenges successfully.
- Shipping Technology: The Must-Have Systems in the Shipper Tech Stack: Logistics and transportation managers now have a bevy of tools at their disposal thanks to the proliferation of tech platforms. However, what tech should shippers implement & deploy to be effective?
- Return to Sender: Maximizing Reverse Logistics Efficiencies: The logistics industry strives to make the manufacturer-to-retailer-to-consumer supply chain as smooth as possible, and they’ve gotten very, very good at it. But can the same be said for reverse logistics?
- 5 Logistics Innovations Supporting E-commerce in 2021: With the recent massive shift to e-commerce, logistics innovations will also experience an increase to support e-commerce transactions in the years ahead.
- Labelmaster Releases Online Training Courses Explaining New South America Shipping Regulations: Labelmaster has partnered with CIQUIME to offer new and exclusive English-language online training courses that explain the new MERCOSUR hazmat transport regulations in South America.
- New Upgrades to Oracle Fusion Cloud SCM Focus on Global Supply Chain Optimization: Oracle has rolled out new updates focused on helping shippers augment global supply chain efficiencies in its Oracle Fusion Cloud Global Supply Chain & Manufacturing (SCM) suit offering, which connects shippers’ supply networks with an integrated suite of cloud business applications.
3PL TECH
- Ten Predictions for Supply-Chain and Procurement Software in 2021: Technology will continue to transform the supply chain moving forward. Check out supply chain and procurement software observations and 2021 predictions.
- Need to Scale Your Online Business? 3PL eCommerce Fulfillment Services Can Help: As your business grows, you don’t necessarily need to invest in more warehouses or staff to handle this growth. There are 3PL fulfillment providers that have the infrastructure to support any sales trajectory.
- How Technology Can Help With Covid-19 Supply Chain Disruptions: Amid the turmoil due to the COVID-19 pandemic, logistics companies are turning to modern technology to gain needed agility and have a better chance of not only surviving but thriving during these volatile times.
Technology & Dangerous Goods Compliance
The COVID-19 pandemic led to a surge in e-commerce sales. It has also brought with it an increase in returns. In fact, online holiday returns were projected to hit $70.5 billion – a 73% increase from the previous five-year average.
As Matt Baker notes in a recent RE Journal article, e-commerce returns are more than double those of brick-and-mortar retailers, and many online stores are willing to eat the additional shipping costs to provide a level of convenience to their customers in order to gain a competitive advantage over the competition. He states, “Online sellers that provide the easiest and most efficient return process will perform the best. They will still provide the convenience of return that retains customers, but do so in a manner that protects their bottom line.”
The returns management process can be especially challenging when goods are hazmat. According to Labelmaster’s Brian Beetz, “Not only are more products being purchased and returned online, more of them are electronics and technology items that contain hazardous components, including lithium batteries.”
Every dangerous goods (DG) shipment carries the risk of being frustrated by compliance gaps – errors in labeling, packaging and/or documentation. Shippers are responsible for getting those details right, which is why a delayed or confiscated shipments can deal a huge blow to an operation’s profitability. Return shipments of DG are subject to the exact same regulations as outbound shipments, which means they can be frustrated by the exact same errors. But with returns, the customer is the shipper, so they’re responsible for shipping those items back to you compliantly.
In short, frustrated return shipments can hurt both your bottom line and your customer loyalty, so you need to make it super-easy for your customers to compliantly return dangerous goods items to you. The best way to make sure your customers can compliantly return lithium battery purchases is to have a comprehensive, well-defined returns management process in place.
To learn more about setting up an effective returns management process, check out The Quick E-commerce Guide to Compliant Dangerous Goods Returns or speak with an expert.
To learn more about dangerous goods software or how to establish a safer, more compliant supply chain, visit https://www.labelmaster.com.
Have questions about dangerous goods transport? Call the Labelmaster Regulatory Hotline at 1.800.621.5808.
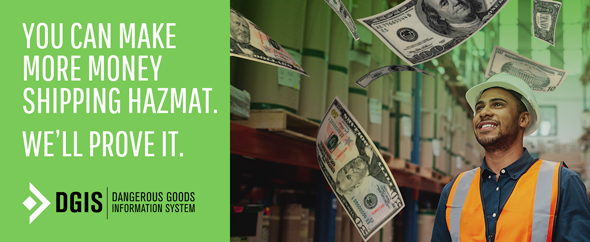
As the industry’s most robust, flexible, and advanced hazmat shipping software, Labelmaster’s DGIS can actually help your operation make more money. DGIS validates shipments and prepares DG declarations so quickly, you can handle more shipments every hour. And more shipments mean more revenue.
Try your own numbers in our calculator to see the added revenue DGIS can generate for you.
