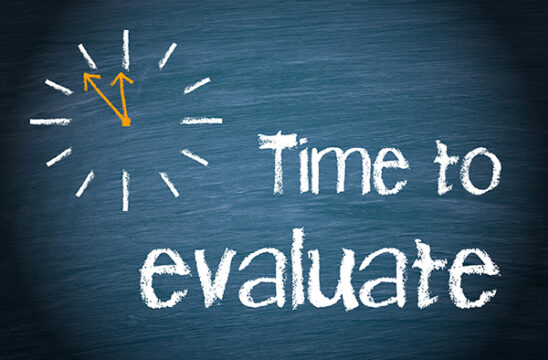
There are two reasons every organization that handles Dangerous Goods must conduct DG training:
- Regulations require that hazmat employees receive function-specific hazmat training.
- Training helps employees do their jobs better, which makes hazmat shipping safer and more efficient.
Most businesses in the hazmat supply chain recognize that #2 is even more important than #1, and understand the value of adapting their training programs to the changing needs of their business.
But how do you evaluate when your training needs to change? And how do you evolve training to get the outcomes your operation needs?
We spoke to some of the industry’s top trainers to get the answers. (We’ll address the first question here and the second question next week.) Here’s what we learned.
How do you know your training needs updating?
According to Labelmaster’s team of consultants and trainers, there are three key indicators that your training program may need to be updated:
- Violations and frustrated shipments
- Changes to your offerings, your teams or the regulations
- Employees who are unable to perform tasks correctly
#1 is fairly obvious. No operation is perfect—a single violation doesn’t mean automatically indicate a gap in your training regimen. But repeated violations or frustrated shipments are a good indication that there’s a gap in your training.
What are you getting cited for? Where are those shipments originating? What do they have in common? Answering those questions will help you pinpoint areas where your training should be upgraded.
Pay attention to changes—internal and external
Changes both internal and external make #2 a little more complex. “Any time you have onboarding of new products, or a change in your business model, you have to take a fresh look at your training,” advises Senior Consultant Alicia Saenz. “Say you’ve gone to a new shipping mode. Ground shipping is less policed than air, but FAA and the airlines are required to report deficiencies. There’s more oversight.”
VP of Operations Pia Jala adds, “Any time there’s a change to the regulations, if you don’t pay attention and update your training, that’s where violations come in.”
Jala also points to the ripple effects layoffs can have on compliance. “People making those decisions don’t always know who the personnel are with DG knowledge. They didn’t know what that person did for the company, so a year down the road they might have violations.”
Create checkpoints for competencies and deficiencies
Of the three main indicators, #3 requires the most analysis. “Look at the competencies you want from an individual. What do you want them to be able to do?” says Labelmaster Senior Manager Jim Shimko. “That requires true analysis and effort at the front end.”
Jala adds, “If it’s one person who has difficulty performing a task according to regulations, they probably slept through the class. But if you’ve documented difficulties time after time, with everyone, it’s a systemic issue.”
That documentation requires some upfront planning. “When you create training, think about things to monitor to make sure it’s meeting your expectations,” says Saenz. “Create checkpoints so after people have gone through training you can get feedback and identify deficiencies.”
Shimko describes a program at a major air carrier. “It’s a three-step process. There’s an evaluation right after class, then another 30 days out to test people’s recall and find gaps. Then there’s a third evaluation three to six months out. That’s how you can truly evaluate whether they’re coming out of training with the skills and knowledge necessary to do their jobs.”
Saenz recommends three evaluation methods for training sessions—student opinion, supervisors’ observations and on-the-job performance improvements, measured by changes in accident rates, injury rates, or penalties.
“In the big picture, you have to get input from employees,” she says. “It all comes down to, do they have the tools they need to do their jobs?”
Does your hazmat training need an upgrade? We can help you evaluate it—call us at 800.621.5808.
Part 2: Evolve your Dangerous Goods training to get the outcomes your operation needs.
Make sure your shipments are safe and in complete compliance with a full line of solutions from Labelmaster—a full-service provider of goods and services for hazardous materials and Dangerous Goods professionals, shippers, transport operators and EH&S providers.