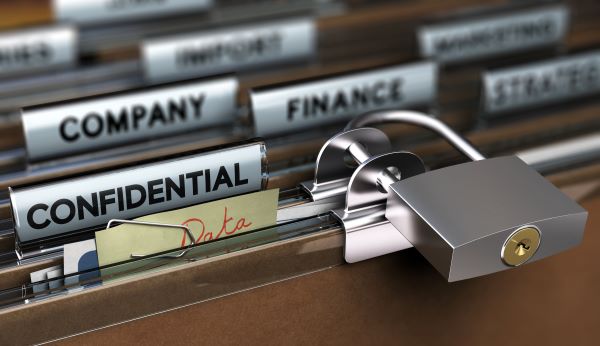
Say you have a building you want to repaint. You contact a distributor who says they can ship you all the paint you need by air, so you’ll have it tomorrow morning. You hire a crew and wait for the paint.
And wait. And wait.
And when you call to find out where the heck your paint is, the distributor apologizes and says they made a mistake—under Dangerous Goods regulations, the paint you wanted couldn’t be shipped compliantly by air. They’re really sorry, but you’ll have it Friday.
You’re never using that distributor again, right?
Those kinds of mistakes happen every day in hazmat transport, and they’re often due to a basic failure—lacking complete, readily available information about a material.
That’s the topic of a recent webinar from Pierbridge and Labelmaster. Listen to recording of this session or continue reading.
The challenge: multiple customers and data systems
The example above was shared by Bob Liva, Senior Account Executive at Pierbridge, who’s one of the leaders of the upcoming webinar. The other leader is Mario Sagastume, Vice President of Software & Customer Success at Labelmaster.
“To ensure a better customer experience,” Sagastume says, “The distributor has to have the information that would tell them they can’t ship that paint by air.”
But this information is pretty basic stuff, right? Why wouldn’t every organization have it ready?
Liva says, “We deal with a lot of third-party logistics operations (3PLs), and often their data is coming from their customers. They all have multiple customers and as a result their means of getting the data would never be the same from one to another.”
Sagastume adds, “They can close a deal on a Wednesday and Thursday they get a spreadsheet that says, ‘Here’s my item number, here’s the quantity, and here’s some basic information about it.’ And then when they’re ready to ship it, they realize it’s Dangerous Goods.”
“And oftentimes they’ll be forced to use the information systems that are in place for the organization they are providing their services for,” says Liva. “So it’s a matter of their employees needing to understand and be familiar with how to operate within each one of those systems. And they’re all different, and nomenclature varies from organization to organization.”
In other words: You are going to need help to gather all the information you need—and keep it current—about every shipment.
Not just about hazmat—or even just shipping
Mistakes that hurt an organization’s customer experience are just one consequence of missing or inaccurate product information. When Dangerous Goods are involved, seemingly small compliance errors can lead to significant costs due to:
- Frustrated or delayed deliveries
- Rejected shipments
- Civil penalties and/or carrier fines
- Costs of manpower and materials to make shipments right
And that’s not even considering the costs involved with mitigating a hazmat incident.
Yet, Sagastume and Liva make it clear that the lack of product information is a problem for all organizations, even if Dangerous Goods shipping isn’t involved.
“This is info you need for billing, for inventory, for procurement—not just for shipping,” says Sagastume. “The more accurate your info, the better off you’ll be.”
Liva adds, “It’s not just about making your life easier, it’s also about making your life less costly and more cost-effective at the same time.”
Sagastume says, “Everybody has a little bit of that information and it has to be looked after just like any other asset in the company. Somebody has to gather it, maintain it, and be able to disseminate it.”
Questions that keep logistics managers up at night
This webinar will talk about much more than simply the information you need to make correct shipping decisions. It will also address these questions that keep logistics managers up at night in the new omnichannel shipping world:
- Which carrier service considerations do you need to take into account?
- What is the right carrier mix?
- How does all the information fit and flow?
- How do you deal with difficult shipping scenarios?
“Dealing with these issues should not just be on warehouse operations alone,“ says Sagastume. “I don’t know of any company that doesn’t share these challenges.”
For a recording of the recent webinar, click here!
Make sure your shipments are safe and in complete compliance with a full line of solutions from Labelmaster—a full-service provider of goods and services for hazardous materials and Dangerous Goods professionals, shippers, transport operators and EH&S providers.