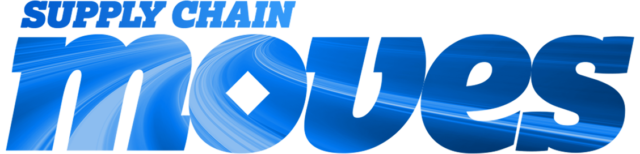

Week of April 13th, 2020
Linking technology news with Dangerous Goods compliance
The supply chain is becoming faster and increasingly more complex. As a result, dangerous goods companies must have the necessary technologies and processes in place in order to make strategic, data-driven decisions, and then effectively execute those strategies.
To help companies keep a pulse on technology trends impacting business and the movement of dangerous goods throughout the supply chain, Labelmaster has launched “Supply Chain Moves,” a weekly report linking the latest technology news to dangerous goods compliance.
Let’s examine the recent supply chain technology and industry news.
TECHNOLOGY
- McKinsey: What is the Future of Automation?: An ever-growing number of logistics and parcel companies are turning to automation to meet the demands of e-commerce. McKinsey examines some of the key reasons why automation is transforming the industry.
- Amazon Off the Cards? Retailers Must Adapt to On-demand E-commerce Solutions: A major shift is taking place as retailer shoulder overweight orders, giving room for agile and disruptive e-commerce solutions to rise.
- How to Make Supply-Chain Data Trustworthy: Organizations on a digital journey are investing in technology and automating processes, but they can’t overlook a critical question: Who is managing the supply chain data?
- Three Ways AI is Shaping the Supply Chain: AI and machine learning have become more common in the supply chain industry. Here are three use cases where they are making an impact.
- Warehouse Management Trends Update for Software Developers: While much has changed when it comes to the supply chain, the one constant is that warehouses need technology to operate efficiently. Here are some of the latest warehouse management trends.
3PL TECH
- Logistics Firms Face Unique Challenges in Their Role as Front-line, Essential Workforce: Logistics workers have seen their workplaces retooled, processes redesigned, and interactions with supply chain partners upended as companies seek to create a delicate balancing act between keeping people safe and keeping on with business.
- Loadsmart, BluJay Integration Gives Shippers Instantly Bookable Truck Rates: BluJay Solutions and Loadsmart’s new API-enabled integration gives shippers instant access to bookable truckload rates and guaranteed capacity.
Technology & Dangerous Goods Compliance
Digital transportation relies on collecting, analyzing and applying complete and accurate data. Unfortunately, that’s a challenge for many organizations.
According to the 2018 Data Quality and Governance Study by the Supply Chain Resource Cooperative, only 15% of respondents believe their existing systems are capable of producing clean data that can be trusted. Furthermore, 75% of businesses indicated that poor quality of data has made it challenging to achieve digital transformation plans.
Stephany Lapierre, founder and CEO of Tealbook, examines the need to effectively manage data in a recent SupplyChainBrain article. She notes that because data comes from a number of sources, and in various forms, “it needs to be ‘processed’ as it goes from its original raw state to a form that people can actually use to do their jobs.”
And, while having data is important, the quality of the data is equally important. Lapierre notes, “High-quality data has strategic value to the enterprise, while poor-quality data can slow things down, send people off in the wrong direction, or stop progress altogether.” She adds, “Supply-chain data absolutely has to be trustworthy if the enterprise is to be competitive. Before this can be achieved, however, someone has to manage the data supply chain itself, drawing on proven resources, improving data collection, and cleaning up the data that has already been collected.”
The findings in the 2018 Data Quality and Governance Study, and points made by Lapierre, are similar to the results of Labelmaster’s 2019 Dangerous Goods Confidence Outlook, which found that:
- 45% of organizations report data collection that’s sporadic, inconsistent or not done at all.
- 55% of organizations say their supply chain partners’ data collection is sporadic, inconsistent or not done at all.
Having complete, accurate master data is the key to streamlining compliant hazmat transport, and it can help unlock efficiencies across all the locations and departments in an organization. However, many shippers don’t know exactly what they’re shipping, and therefore don’t have the necessary master data, which has a profound ripple effect on the entire supply chain.
To learn more about having the data necessary to maintain an efficient and compliant dangerous goods supply chain, check out Labelmaster’s blog post, What is Master Data, and Why is it so Important for Hazmat Transport?
To learn more about dangerous goods software or how to establish a safer, more compliant supply chain, visit https://www.labelmaster.com.
Have questions about dangerous goods transport? Call the Labelmaster Regulatory Hotline at 1.800.621.5808.

Labelmaster’s Dangerous Goods Information System (DGIS) is the leading SaaS solution to help companies more efficiently and accurately manage their Dangerous Goods shipments. DGIS validates your Dangerous Goods shipment data against the latest regulations, ensuring a more efficient supply chain and reducing friction found in Dangerous Goods shipments. DGIS is a certified partner/validation solution with ERP, transportation and warehouse management systems.
