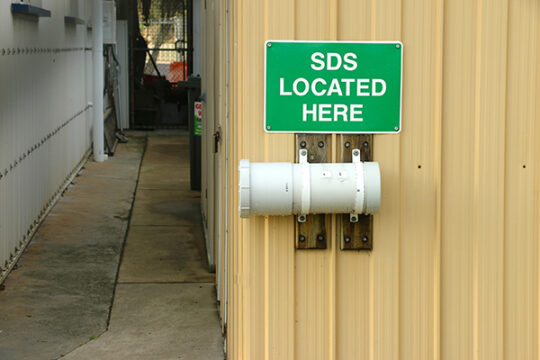
Sometimes, we overlook the obvious. I was working with a client just last week and was asked to evaluate a pair of materials for further handling at a new site they are developing.
“Will you please send me the Safety Data Sheets? I’ll take a look and run the numbers,” I said. A few minutes later my email pinged in with … twenty-year-old Material Safety Data Sheets, or MSDS’s. Ouch!
When I contacted the client, they explained that the materials had been “in inventory forever” and no one had though to update the data sheet library. Suddenly, a new task was required for the client.
Fortunately, we offer resources to help with this issue. But here’s the background.
The problem with MSDS’s
The Occupational Safety and Health Administration (OSHA) was established in 1970—fifty years plus back now—in order to help protect American employees from dangerous conditions in the workplace. OSHA governs this vital area via the 29 CFR 1910—the set of regulations that establish a large number of rules specifying everything from how ladders should be used and maintained to how to rig cranes and be safe around electricity.
One very important part of the regulations that relates directly to the client incident I related above is found in 29 CFR 1910.1200; this is the HCS, or “Hazard Communication Standard.” As its name suggests, its purpose is to establish a set of rules under which employers are required to inform employees about the hazards of chemicals found in their respective workplaces. A version of this rule has been in place since 1983, and it set the initial requirement for the MSDS—the Material Safety Data Sheet.
An MSDS was a set of data gathered in one easy place that outlined the known and suspected hazards of the material, as well as information about how to store, handle, and clean up the material. MSDS were useful documents to have and could be very helpful, but one big problem with them was their inconsistency of information. While one MSDS might be extremely detailed and informative, the next could be sparse and meager. The rule did not specify content in a way that truly established completeness and uniformity.
The standardized Safety Data Sheet
So matters stood until 2012. In that year, OSHA published its revised HCS. This new iteration of the standard follows the International Standard for Chemical Hazard Communication known as the Globally Harmonized System, or GHS. The 2012 HCS established new standards for labeling of containers, training of employees, the maintenance of a written safety program—and the subject of this blog, the conversion of existing MSDS’s into the new format Safety Data Sheet, or SDS.
The GHS is a UN program that is all about standardizing the presentation of information across the nations of the world; transport professionals are familiar with this idea through the use of the UN Model Regs and its offshoots in the ICAO TI, IMO IMDG Code, EU ADR, and our own 49 CFR. They’re all intended to make it simple for a DG professional in one place to easily communicate the hazards of a shipment to a DG professional in another place.
The same idea is embodied by the GHS for workplace chemical hazard communication. Everything: Labeling, Safety Data Sheets, symbology, etc., is standardized. SDS’s are to be presented in a 16-section information format that contains a far greater amount of data than was ever specified for the old MSDS format. While an old MSDS may serve as a good starting point to convert and revise over into an SDS, there may be a great deal of work involved to find absent information that is now needed. Also, sometimes chemicals change over time. An MSDS that was current a few years ago may lack critical updated information. The new SDS will need revisions to feature this updated information.
SDS conversion and generation
If your “data sheet fleet” still contains MSDSs instead of SDSs, there’s bad news: the transition period that allowed for conversion over to the new system ended back in 2016. Five years down the road in 2021, your library should be fully up to date. If it isn’t, there can be consequences. Apart from the obvious matter of an OSHA citation, it’s also not legal to transport shipped containers unless a compliant SDS is available for the material contained. No one wants their materials legally “stranded” at your site because you lack the proper documents.
And of course, it’s a safety matter as well. If someone experiences an incident with a chemical and is injured, or a spill or unintended release occurs, it’s imperative to have the best, most complete information available to help address it and to pass to first responders. A compliant SDS will be your go-to for each of those needs.
When would you need to generate a new SDS? If you receive a chemical (or create one) that falls under the classifications as a hazard in Appendix A or B of the 29 CFR 1910.1200, and there is no-pre-existing SDS, then you’d need to run the chemical through the classification criteria in the appendices. If it meets the criteria of one or more classes as a physical or health hazard, and if the material is NOT exempt from the rule, an SDS would need to be created.
Need help with these processes? Read on.
Modernizing your “data sheet fleet”
If your company needs to convert old MSDS’s to SDS’s, or generate new SDS’s, where to turn for help? If it’s a big fleet, it can be a big job. Even smaller libraries can be intimidating to folks that may lack the time to engage in the effort necessary to convert over, or who perhaps feel that their understating of the new requirements is less than complete.
Thankfully, there is readily available help. Labelmaster partners with a specialist in this field: Quantum Compliance. Quantum is a recognized authority in the field and has unique ability to evaluate your fleet of data sheets, parse through which ones may need help, revision, or outright replacement, and help you plan and execute a strategy to do it. Quantum can support you in this effort, or take charge. Just like your relationship with Labelmaster, Quantum will be there in whatever capacity you require.
The client I mentioned at the beginning of this blog is now busy checking out their data sheet library to see if they need more help. If they do, Labelmaster and our partner Quantum stand ready.
Do yourself, your employees, and your compliance posture a favor; get current now. Don’t be OSHA’s next hazard communication citation.
Make sure your shipments are safe and in complete compliance with a full line of solutions from Labelmaster—a full-service provider of goods and services for hazardous materials and Dangerous Goods professionals, shippers, transport operators and EH&S providers.
Hi Nikki,
could you please provide some reference to your statement : “it’s also not legal to transport shipped containers unless a compliant SDS is available for the material contained”, as best to my knowledge a SDS is not a required document for transportation. The SDS is a document required by OSHA, but not by DOT. If I am off base here, I would like to know, so that I can adjust my training accordingly.
Hi Torsten,
It’s a matter of perspective. OSHA requires under the 29 CFR 1910.1200 HCS that inner containers shipped from a facility are labeled and have a valid SDS available and that the SDS is provided to the downstream end user. However, since OSHA has no authority over DOT functions, there is no legal requirement to include an SDS with a shipping paper, or in the box, etc. In other words, DOT does not enforce anything about them, or about HCS (GHS) labels. Nevertheless the requirement from OSHA must be satisfied, so an SDS is very often sent with the first shipment to an end user, or emailed, or whatever.
Thanks,
Nikki