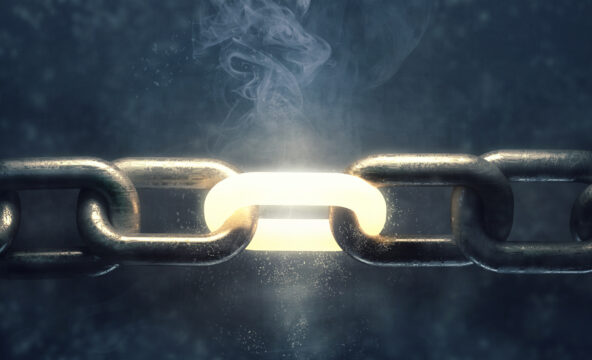
Very few organizations maintain their own end-to-end supply chains—we all depend on partners to some extent. That’s why it was disheartening to learn, in the 2019 Dangerous Goods Confidence Outlook, that so many hazmat pros had so little confidence in their supply chain partners:
- 71% of respondents wished their supply chain partners were as compliant as their own company.
- 52% called the quality and accuracy of data provided by their supply chain partners “sporadic and inconsistent.”
With millions of Dangerous Goods shipments crossing the globe every day, no one has the time or resources to double-check everything received from a supply chain partner. That means errors in one link of the chain inevitably get passed along, making incidents and accidents more likely.
We spoke with DG and EH&S pros in the pharmaceutical and aviation industries about their experiences with supply chain partners and how they’ve worked to improve them. Here’s what they said.
Compliance is “always on the shipper”
One obvious concern with supply chain partners who may not be as compliant as your organization is that their compliance gaps may go undetected—until an inspector holds up your shipment.
“When a shipment is out of compliance, it’s always on the shipper,” says a DG compliance manager for an aviation company. “That’s why we make a classroom out of our receiving dock whenever suppliers have shipped us items that were incorrectly packaged or labeled.”
Andrew Wolff, EHS Technical Manager at Baxter International, says, “It’s important that everyone at our facilities understands the shipping requirements. That way, we’ll never be in a position to have to say ‘When we received it, it didn’t have any of that.’”
“Ultimately, what we make goes into someone’s vein,” says Takeda Pharmaceutical Company Director of Environment, Health & Safety Obed Varela, MSc, CSP, CHMM, REHS. “If we had a supplier that wasn’t compliant, they wouldn’t be in business with us for very long.”
Data problems can be “a constant headache”
Compliance is only part of the concern with supply chain partners. A more common issue is that data about a shipment’s contents can be incomplete, inaccurate or outdated, leading to a non-compliant or even unsafe shipment down the chain. Yet, for a variety of reasons, safety data sheets (SDS) are frequently inaccurate.
“Composition changes drive the vast majority of SDS errors,” says Dimitri Hollis, Global Product Stewardship Manager, Corporate EHS at Takeda Pharmaceutical Company. “Changing a range, or adding more or less of something, can significantly impact the SDS. Those changes can affect classification and packing group, or even move the item to a different hazard class or introduce a second hazard.”
“One of the big gaps we encounter is about inner container air pressure testing,” says the aviation company compliance manager. “We’ll get something shipped to us by ground, so of course they don’t care about air pressure testing, but we need to know if the inner containers meet requirements. If we don’t know, we have to use supplemental packaging when it might not be necessary. It’s a constant headache, and expensive, too.”
He adds, “If the SDS is wrong, with so many people down the chain relying on it, there’s a higher likelihood of errors—along with incomplete emergency response information if there’s an incident.”
“Start that conversation” with supply chain partners
How can you improve the accuracy of your own hazmat data, as well as the compliance and data you receive from your supply chain partners?
Hollis says, “You can only be responsible for your own organization, but it’s important in a large global company to have visibility into every area. We do supplier audits to see if they have the processes in place. It’s wise to start that conversation, and beneficial to both parties to highlight any gaps and eliminate unnecessary risk.”
“It can be a struggle to keep accurate inventory at your site,” says Varela. “We physically go through areas to verify names, amounts, locations and other data, and reference those against our SDS list.”
“We have a policy where, anytime we disagree with Section 14 of the DG shipper’s declaration, we reach out to the manufacturer,” adds the aviation company compliance manager. “If that manufacturer isn’t disclosing enough information, we go back to them for additional information.”
While most supply chain partners are willing to work with you to improve compliance and data quality, you have the ultimate leverage.
As Wolff says, “I have experience working closely with suppliers to ensure regulations are fully met. It’s my job to make sure they know we’re always going to do things right.”
Need help with a database cleanup, compliance assessment or other ways to make your organization a better supply chain partner? Call us at 800.621.5808.
Make sure your shipments are safe and in complete compliance with a full line of solutions from Labelmaster—a full-service provider of goods and services for hazardous materials and Dangerous Goods professionals, shippers, transport operators and EH&S providers.