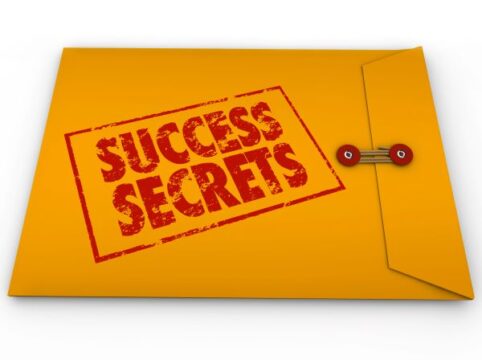
By Katy Schroedl, ProShip, Inc.:
With hazardous material shipments accounting for roughly 20% of the total volume of all shipments, Dangerous Goods (DG) shippers recognize the value in these shipments. While DG shipments can seem to be a complex and restrictive subset of the supply chain, they are a necessary challenge for so many brands today. Many struggle with:
- The timely process to manually update to the latest regulations to ensure compliant labeling, packaging and documentation
- Costly penalties and stopped shipments related to compliancy gaps
- Providing trackable savings to the department
DG shippers who have automated and streamlined their hazmat process understand that you cannot jump into these shipments without some prep work, especially with the cost and legal liabilities involved. Having a detailed processes in place as well as implementing an automated technology to back it, are just two of the many initial steps to running a compliant and comprehensive DG program.
To continue your journey to understanding hazmat shipping compliance, here are four secrets from DG shippers who compliantly perform thousands of hazmat shipments each day.
1. Flexibility will be the lifeblood of your system.
It’s hard to see the words “flexible” and “hazmat shipping” in the same sentence, but flexibility is key to adjust quickly to the changing environment. Regulations for DG shipments change often, so a system that can adjust quickly will support your supply chain as it navigates DG. With a DG program that can adapt rapidly, your operations won’t experience downtime and will be minimally impacted by updating regulations. When your Multi-Carrier Shipping Software (MCSS) also offers the flexibility to scale as your needs change, your complete solution becomes customized to your business needs, no matter the complexity or specific nuances.
2. Omnichannel extends to DG shipments as well.
Omnichannel fulfillment strategies are completely necessary to satisfy the weight of customers’ growing expectations. 2-day shipping no longer ensures a positive Customer Experience (CX) as the goalposts on customer expectations are continuing to move. Brands need the technical functionality that facilitates consistent and compliant DG shipment processing across multiple locations. With a DG program that has the option to shift processes to other inventory or fulfillment locations, brands can optimize their supply chain to delight customers while ensuring that compliance is still maintained – no matter the location. The connections in your Enterprise Software Stack (ESS) through a MCSS allow for a streamlined shipping journey in any of your omnichannel fulfillment locations, bringing the product closer to the customer and shortening its time in network.
3. Connect the dots with systems now to avoid starting over later.
With so many different technologies in the ESS, it’s important to check that your systems integrate seamlessly and accurately. A DG system is one piece of the puzzle, but if this part isn’t connected to everything else, inefficiencies creep in. Responsive integration among the ESS is important to optimize operations and reduce inefficient processes. When information and processes are shared within a MCSS, it eliminates the need to look up regulations and automatically updates to maintain compliance. As the information is validated and returned to the server, shippers are provided compliant labels and documentation through an automated solution that simplifies and reduces costs within your supply chain. Check out this technical diagram explaining the Hazmat Process Model.
4. Compliance is a requirement and not an option.
This secret completes the circle for the past 3. When you implement complementary systems and processes at all your inventory and fulfillment locations, all location can respond compliantly to a surge in demand, whether that is planned or unplanned. With last year’s consumer spend topping $204 billion during peak season, making a mistake during this busy season because of a lack of preparation could be costly. Finding a partner who understands this and can help you prepare now will ensure a timely, compliant and reliable solution during the upcoming peak season, as well as those to come.
Many brands utilize a DG partner who can simplify and streamline hazmat shipping for them. At ProShip, that means Labelmaster, our Dangerous Goods partner who supports our customers to effectively, securely and compliantly ship hazmat. When you utilize the Labelmaster software module within ProShip’s Multi-Carrier Shipping Software solution, you not only save time and elevate your business, but your shipments maintain compliance throughout the labeling, packaging and documentation processes.
Top resources for shipping dangerous goods:
- [Webinar] Living Dangerously: Demystifying Hazmat Shipping
- [Podcast] ProShip ParcelCast: Do This, Not That: Dangerous Goods Shipping 101
- [Brochure] ProShip + Labelmaster
Reach out now to find out more about partnering with Labelmaster for all your DG needs. The combination of ProShip x Labelmaster ensures automated, complete compliance for an efficient and cost-saving supply chain solution.