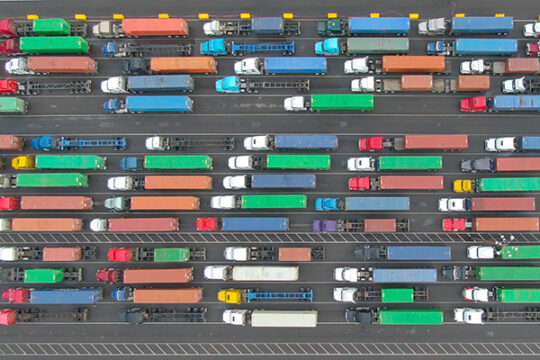
Two things most shippers are (or should be) keenly aware of right now:
- The global supply chain is enduring disruptions like we haven’t seen in decades.
- The holidays are coming.
Yes, we’re heading into peak shipping season—which strains supply chains even in the best of years—at a time when inventories are already thin, shortages strike with no warning, and no one seems to know what’s going to go wrong next.
In this environment, you’re probably doing everything imaginable to make double- and triple-sure your shipments reach their destinations on time. The last thing you need is to have a shipment delayed or returned due to a Dangerous Goods compliance failure.
Here are some common hazmat shipping errors every shipper needs to avoid this holiday season.
Shipping hazmat without knowing it
The explosive growth of eCommerce has amplified opportunities for thousands of entrepreneurs and created millions of satisfied customers. It’s also multiplied the numbers of people and organizations who simply don’t know they’re shipping hazmat.
Some popular eCommerce items that may be classified as Dangerous Goods include:
- Lithium batteries and battery-powered devices
- Nail polish and other cosmetics
- Paints
- Adhesives
- Aerosols
- Fireworks and flares
Here’s some basic advice for newer shippers and manufacturers: Check the safety data sheets (SDS) for every ingredient and component of everything you ship. (You should be able to obtain them from their original manufacturer.) The SDS will tell you if that material is regulated as hazmat, and if so, its class and UN number. That information, in turn, will let you research compliant shipping practices.
You can also find helpful hazmat shipping information on the websites of most major carriers and eCommerce platforms.
Finally, a note for more experienced shippers, 3PLs and others: Your less experienced supply chain partners may need help identifying hazmat and shipping it compliantly. We’re all ultimately part of the same supply chain, and compliance helps keep everyone safer.
Making mistakes with labels, marks and documentation
Simple errors in labeling, marking and documentation are a major cause of delayed or returned shipments. The first thing an inspector sees are the labels and marks on the exterior of your package. If they don’t align with the documented contents, there’s a good chance that shipment will be held up.
Hey, we get it. The regulations governing hazard communication and documentation are complicated, and they change with distressing frequency. The regulatory manuals for shipping Dangerous Goods run to more than 1,000 pages—each. It’s a lot of detail to keep straight, and with the added pressure of fulfilling holiday orders, people can get details wrong.
Shippers can ensure compliance—and save time on every shipment—by using advanced Dangerous Goods software such as Labelmaster’s DGIS.
Using labels and placards that can’t handle the elements
In parts of the northern hemisphere, the holidays also happen to bring some of the worst weather of the year. In other parts of the globe, supply chains must cope with glaring sunlight and stifling humidity. Dangerous Goods labels and placards have to endure these harsh elements—and, with supply chains slowed by disruptions and heavy holiday traffic, they may have to endure them longer than usual.
And that’s where you’ll find another cause of compliance failures. When labels peel off, or the ink runs on a placard, shipments get rejected.
That’s why Labelmaster offers hazmat labels and placards that endure the harshest conditions the supply chain can dish out. Rocky Mountain blizzard? Muggy Florida warehouse? Searing desert heat and sunlight? With extreme conditions labels and placards, they won’t affect the compliance of your holiday shipments.
Neglecting reverse logistics
Almost one in three products ordered online are returned—and for electronics, that number is even higher. If those products contain Dangerous Goods, the return shipments are subject to the same regulations as the original shipment. Only, in the case of a return, it’s a customer doing the shipping, and that customer has no hazmat training.
Today’s eCommerce customer expects—demands—a painless return process. Shippers who don’t lay the groundwork for easy, compliant returns of items containing Dangerous Goods will not only have to deal with added delays and costs, but also with seriously disgruntled customers. And what shipper wants that during this incredibly challenging holiday season?
Having sound reverse logistics processes in place is especially essential for products containing lithium-ion batteries, such as cell phones, laptops and handheld games—which may even require special packaging.
The next few months promise to be stressful, for you and everyone else in the global supply chain. We recommend doing whatever it takes to make sure you’re not adding to that stress with easily avoidable hazmat compliance errors.
Need answers to your hazmat questions? Call the Labelmaster hazmat hotline—1.800.621.5808, 8 a.m. to 5 p.m. Central, Monday through Friday—and speak with one of our experts!
Make sure your shipments are safe and in complete compliance with a full line of solutions from Labelmaster—a full-service provider of goods and services for hazardous materials and Dangerous Goods professionals, shippers, transport operators and EH&S providers.