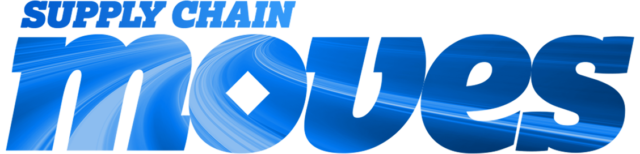

Week of May 29th, 2023
Linking supply chain news with dangerous goods compliance
Labor shortages continue to be a challenge across the supply chain. This has businesses looking to further automate their processes and optimize their existing workforce.
Let’s examine some recent industry news.
SUPPLY CHAIN NEWS
- Understanding America’s Labor Shortage: The Most Impacted Industries: The health services, professional and business services, trade, and accommodation and food services industries have the highest numbers of job openings.
- People Remain Stumbling Blocks to Procurement Success: Technology is great, but people continue to be the largest roadblock to procurement performance, according to a recent survey.
- Transportation Labor Gets Biden Administration Attention: Transportation leaders from government and industry are closely watching labor negotiations that hold consequences for the nation’s supply chain.
- America’s Semiconductor Boom Faces a Challenge: Not Enough Workers: Strengthened by billions of federal dollars, semiconductor companies plan to create thousands of jobs. But officials say there might not be enough people to fill them.
- Virtual Reality Helps Tackle Workforce Shortage: Manufacturers, hotels and other businesses have increasingly turned to virtual reality to help train their staffs amid a growing labor shortage.
- The Forever Labor Shortage: The coming surge in boomer retirement will create a labor shortage that will last for decades.
OUR PERSPECTIVE
- Manual compliance processes waste workers’ time. Many tasks are required to put a DG item into transport, so slow compliance processes result in slower supply chain operations, especially for organizations constrained by staffing issues. Relying on manual processes wastes workers’ valuable time by having them repeat routine tasks such as researching DG shipping information or creating compliant documentation. Those wasted minutes impact the overall efficiency and make it more difficult to overcome potentially costly disruptions.
- Automation helps optimize labor. By automating DG processes, tasks are performed more quickly and with fewer delays, allowing workers to handle more hazmat shipments in less time or devote more time to higher value activities. Making team members throughout the supply chain more efficient helps businesses grow without having to add more personnel, thereby supporting better staff utilization and helping offset labor shortages.
- Training is still important. Even with increased automation, training is still required for employees involved in the shipping and handling of DG. Adopting a modern, technology-driven approach to hazmat training through eLearning helps businesses quickly and effectively train and recertify employees.
To learn more about dangerous goods software or how to establish a safer, more compliant supply chain, visit https://www.labelmaster.com.
Have questions about dangerous goods transport? Call the Labelmaster Regulatory Hotline at 1.800.621.5808.