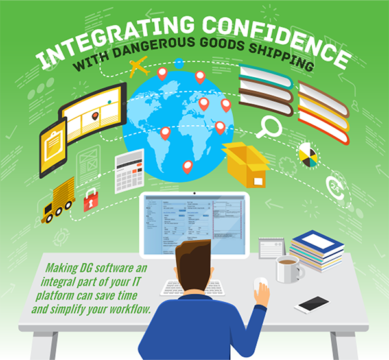
If your weekly grocery shopping includes both meats and produce, life’s a lot easier if you can buy them at the same store.
If your exercise regimen includes both weight work and swimming, life’s a lot easier if your health club includes a weight room and a pool.
And if your operation ships both non-regulated materials and Dangerous Goods, life’s a lot easier if you can process both kinds of shipment from the same platform, on the same screen.
That’s why so many organizations automate their hazmat shipping compliance by integrating our DGIS solution with their ERP, TMS, WMS or other automation platforms. Integration doesn’t just make their lives easier—it also makes their operations more agile and more competitive.
Integrating DGIS with your automation platform can be a gamechanger. But how do you make it happen? Read on.
Why DG software integration is more essential than ever
To be competitive in today’s global, multi-modal, need-it-tomorrow supply chain, it’s more essential than ever that your DG software be integrated with your automation platform.
Being able to process, document and validate hazmat shipments in the same workflow as your non-regulated shipments gives you:
- The speed and simplicity you need to keep up with eCommerce, with instant access to the right product data and validation technology helping you process shipments in seconds (instead of minutes)
- The ability to smooth over supply chain disruptions that seem to happen every other week
- Opportunities to grow new revenue streams from new items, new modes, new destinations and new locations
- The confidence in your compliance you need to grow your business without being held back by fear of the consequences of non-compliance
DGIS integration means your teams never have to exit the platform they use every day to get real-time validation based on the latest DG regulations, carrier variation accountability, a training records library, storage of DG parts data (including DG-required fields and non-DG parts classification), labeling diagrams, packing instructions and more.
Here’s how to make it happen, based on the automation platforms you already use.
DGIS integration if your platform is already a DGIS partner
Please take a minute to look at our DGIS Partners page. You’ll see a dozen or so platforms listed, from major carriers to enterprise-level ERPs to some of the most advanced TMS and WMS platforms available. If a platform you already use is listed there, you’re that much closer to integrating DGIS with your everyday workflows.
Here’s what needs to happen now:
- Connect with your IT team* and tell them you’d like to activate the platform’s DG functionality.
- Your IT team will contact your vendor to enable DGIS integration via an application programming interface (API). The API is simply a set of computer code that lets your platform “talk” to DGIS when your shipments contain hazmat, so DGIS can display all the relevant information within your platform. (As an example, you may already use other APIs in connection with the banking or social media apps on your smartphone.)
- You’ll work with your vendor and Labelmaster to help the platform identify hazmat shipments. This is where you leverage your master data—complete, detailed information about the components, makeup, dimensions and origins of everything you ship.
- Your vendor, your IT team and Labelmaster will complete the integration. Once your platform knows how to identify hazmat shipments, it will automatically pull up DGIS fields for every shipment containing hazmat. You’ll never have to switch screens for DG processing again!
*You may also need to work with your management team to authorize DGIS activation, which is not cost-free. The process often requires a separate contract. The section above can help you make the case that DGIS integration is a value-add that gives your operation a strong competitive edge.
DGIS integration if your platform is not a DGIS partner
If your current automation platform is not listed on our DGIS Partners page, you can still integrate it with DGIS. It just takes a few different steps:
- Contact Labelmaster and let us know you’d like to integrate DGIS with your automation platform. (You should also contact your platform vendor, who may find our DGIS Web Services page helpful.)
- Labelmaster will work with your platform vendor and your IT team to determine whether there is sufficient compatibility to allow DGIS integration. If so, we’ll continue to collaborate to create and activate the API that lets your platform “talk” to DGIS when your shipments contain hazmat, so DGIS can display all the relevant information within your platform.
- You’ll work with your vendor and Labelmaster to help the platform identify hazmat shipments. As above,this process leverages your master data to “teach” your platform which shipments contain hazmat, so it knows when to access DGIS via the API.
- Your vendor, your IT team and Labelmaster will complete the integration. Your platform now will automatically pull up DGIS fields for every shipment containing hazmat, so you can achieve agile, confident compliance within your everyday workflows.
*As mentioned earlier, you may also need to work with your management team to authorize DGIS integration, which is not cost-free. The section above can help you convince them that the agility and confident compliance you’ll get with DGIS integration makes it worth every penny.
Maximum compliance with minimal disruption
Integrating DGIS with your automation platform is an essential step for staying competitive in today’s supply chain. The ability to process hazmat shipments with the industry’s most advanced DG software helps you avoid the delays and costs of non-compliance, and doing so within your everyday workflows gives you maximum compliance with minimal disruption.
Ready to see what DGIS integration can do for your operation?
Make sure your shipments are safe and in complete compliance with a full line of solutions from Labelmaster—a full-service provider of goods and services for hazardous materials and Dangerous Goods professionals, shippers, transport operators and EH&S providers.